A manufacturing process management system has been developed to centrally manage the entire manufacturing process from order receipt to production.
As the instructions from order to production process were almost entirely analogue and thus belonged to the individual, a system was developed to centrally manage them in the form of data.
All workers can now check the status of their work, and as a result of improved efficiency, sales have doubled.
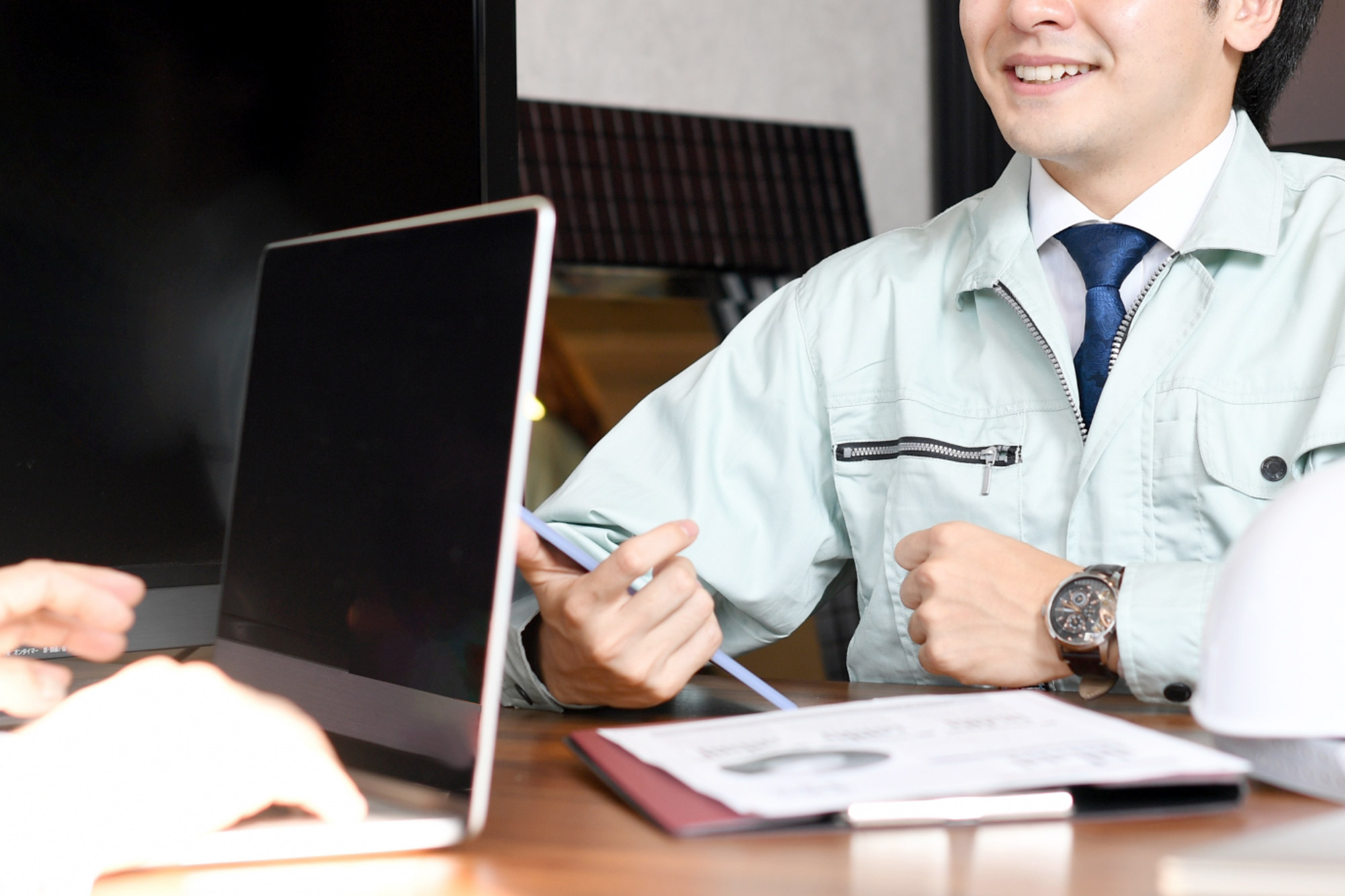
- Development Systems Manufacturing process control system (estimated development cost: approx. 4 million yen).
- type of industry Manufacturing (employees: approx. 20 / location: 1)
- old management method Access/Excel/Handwritten.
Troubleshooting
- As handwritten instructions were physically passed around the manufacturing process, it often took dozens of minutes to find the instructions when changes were made.
- There were about 200-400 replacements of instructions (changes to orders) per week, which meant that time had to be spent on replacement work two or three days a week.
- In some cases, orders were placed with outsourcing companies, but delivery was accelerated and the company had to manufacture the products in-house, resulting in a surplus of products for outsourced manufacturing.
Issues not recognised
- Almost all operations are analogue, so only the person in charge is aware of the content. (gerrymandering)
- Manufacturing was inefficient, as orders were received and manufactured from items that were close to their delivery date.
- There were discrepancies in the information grasped by the clerks and the information grasped by the person in charge of the factory. (Information not shared)
Solution A manufacturing process management system was developed to clear information sharing.
Since everything from order receipt to the manufacturing process was gentrified, a system was developed to centrally manage it with data.
Anyone can now check the status.
As a result, it became possible to manufacture the same products in batches, with orders received and delivery dates close together, and sales have doubled.
Every week, the instructions had to be replaced due to changes in order details, but this has also been eliminated.
The clerks are now able to spend their time on other tasks, so there is no need to hire one more clerk.